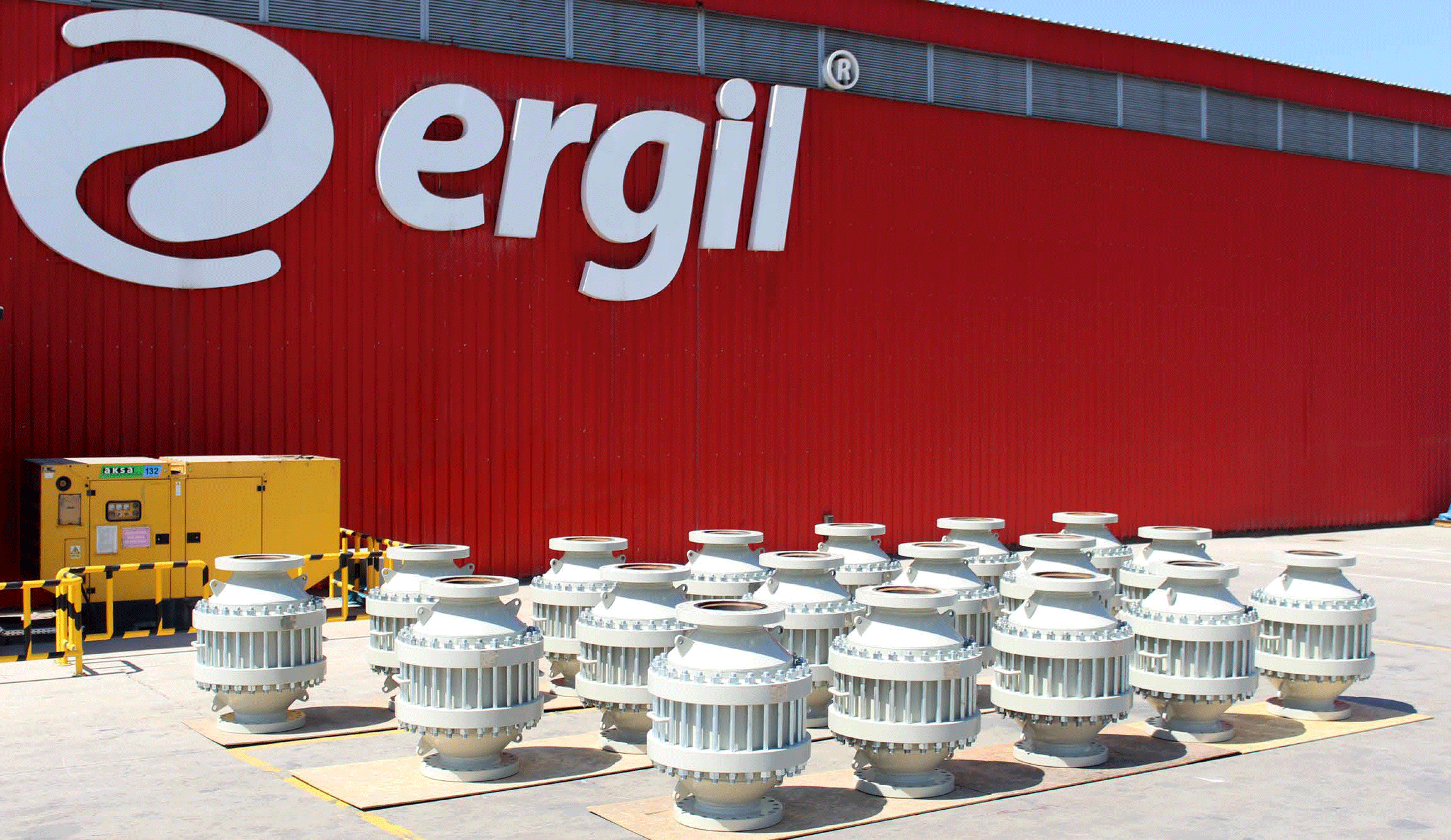
Project Overview and Challenge
In 2009, Gazprom and Srbijagas signed the Agreement on setting up a joint venture for the BanatskiDvor UGS facility. The BanatskiDvor UGS facility is one of the largest gas storages in Southeastern Europe. The facility was commissioned in November 2011. With a working gas capacity of 450 million cubic meters, the UGS facility has a maximum gas deliverability of 5 million cubic meters per day.
In this kind of plants or projects that have many critical processes and equipment, safety of the environment carries high importance. At the end of the day, energy source which is being carried by the pipeline is used by the people, manufacturers and houses; that brings a great requirement for the consistency of the system. Another issue is, any accident there occurs might create a serious damage for both equipment and the people. It is understood that any investment to provide the safety of the system is essential.
Flame arrestors are basically items which are used to prevent fire or spreading the fire into the systemby blocking the flame with its special designed structure. They are one of the best ways to ensure the system safety. On the other hand, when the size of the pipeline and the overall system gets enlarge, it is being more complicated to design and fabrication of a flame arrestor. The biggest challenge for this project is size of the project and international certificate requirements. That creates a requirement for both dedication for the production stage and also quality inspection to be able to catch the international safety standards.
Action
Storagetech™ custom-made 16” In-Line Flame Arrestors are passive devices that prevent the propagation of a flame or fire from entering into an opening in a pipeline or vessel discharging flammable vapor.
There are some factors and features that make this project unique and challenging. Here are some of them
- 16’’ 600# connection
- II A Safety Group
- Working ability under high pressure and lower temperatures
- 1850 kilograms size and ability of design and fabrication them within our engineering and manufacturing capacity.
- Supply of ATEX certificate for the big size such as 16’’
- Compatibility with PED Certificate
- AD 2000 Standards
- Special design for the system requirement
- Delivery on time
- Full accordance for the customer need
It also takes the 16 weeks to deliver the whole project, on the other hand; 31 pieces custom design 4″ In-Line Flame Arrestors (CS), 3 Pieces custom design 6″ In-Line Flame Arrestors (SS316), 1 piece custom design 8″ In-Line Flame Arrestors (SS316) have been supplied to that project.
Result
With the supply of this project, customer ensures the system safety and prevents the possible accidents that may result with the financial or humanitarian loss. These products, especially 16’’ one are not the items you can make produce in any of the manufacturing plant and workshop. This group of products requires sensitive and dedicated work with a great engineering expertise.
Another successfully completed phase is consistent collaboration with customer because tailor-made work is required in this project. Due to its not-plug-and-play nature of the product, understanding customer requirement is essential part. It also requires a meaningful partnership with customer and also between different departments such as sales, engineering design, pricing, production and project coordination. We successfully completed this phase and finally can provide customer satisfaction.
Please Click for the PDF Format: Case Study of 16’’ Flame Arrestor for BanatskiDvor UGS Facility