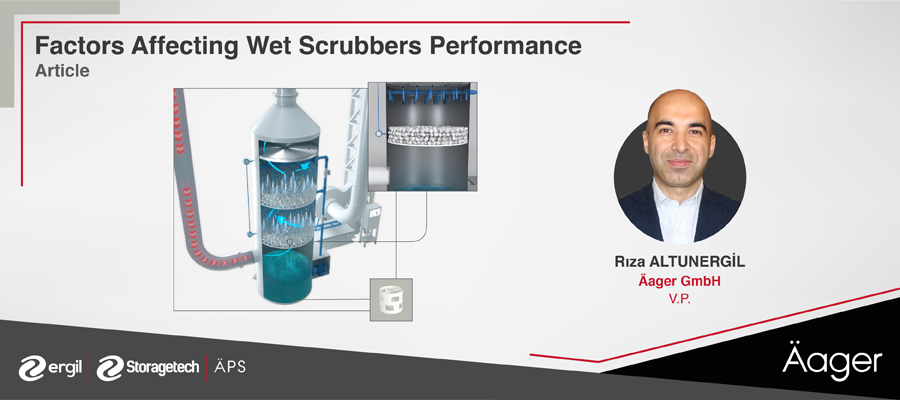
Wet scrubbers work to abate chemical emissions from process equipment. However, these devices do not perform the desired emission results, and they need to be frequently turned off because of problems. Research identifies several factors contributing to the inefficiency of wet scrubbers. Some of these issues include accumulation of solids, biological growth, channeling due to plugged spray nozzles and rectangular housings and poor air distribution, disproportionate velocity profile considerations, inadequate liquid flow, incorrect addition of scrubbing liquid, wrong pump size, the inadequacy of sump fluid replacement, incorrect position of the pH probe, liquid re-entrainment, insufficient packing depth, plugged beds or mist eliminators, and poor gas-liquid contact (Kastner & Das, 2002; Yap, 2005; Danzomo et al. 2012; Hankinson, 2018; the United States Environmental Protection Agency, 2021). Other studies expressly point to the cooling pads, including their size, surface area, and thickness (Sreeram, 2015). These problems indicate poor design and operation, which contribute to the inefficiency of the wet scrubber. However, Yap (2005) and Danzomo et al. (2012) identify atmospheric conditions as contributory factors to performance. Kim et al. (2001) refer to other conditions, which they classified as operational. These conditions comprise droplet size, liquid-to-gas flow ratio, and velocity of the falling droplet. The following issues illustrate specific design inefficiencies.
Accumulation of solids
The accumulation of solids hinders scrubber performance. These solids include encrusted salts and polymers, which collect on mist eliminators. In addition, insufficient mist disentrainment and vapor-liquid contacting, and pressure drops ruin the internals of the scrubbers.
Biological growth
Algae growth builds up in mist eliminators and packed bed sections, which results in inefficient scrubber performance. In acid scrubbers, biological growth is expected when pH is usually retained at 8 to 9 (Hankinson, 2018). If not dealt with, the growth results in channeling areas and intensify the scrubber pressure drop.
Channeling due to plugged spray nozzles
Plugging causes shutdowns in scrubbers with spray nozzles. It disables the packing area to receive liquid and produces no absorption in an area. This issue reduces the scrubber’s efficiency.
Channeling due to rectangular housings and poor air distribution
Incoming air-streams in vertical scrubbers abruptly turn 90 degrees into the packing. Only a few scrubbers account for this sudden turn. Since airflow must trail the path of least resistance, the air continues straight to the inlet up to the vessel’s back wall in this design. The air is disturbed and shall spiral and whirls up to the packed bed section. Dead spots occur within the packed bed due to this channeling. As a result, air velocity is higher, though lower than the intended retention time. In rectangular scrubber housing, air follows a similar undisrupted path; however, dead spaces are common. Design accounts for air distribution efficiency.
Disproportionate velocity profile considerations
Velocity restrictions play a significant role in scrubber performance. Once scrubbers are operating, the cross-sectional area is fixed. A scrubber’s efficiency decreases when the device’s design is for 10,000 CFM and the fan exhausting at 14,000 CFM. At this design combination, the pressure loss rises. The mist eliminator performance reduces with a mismatched velocity profile, affecting the evaporation and absorption losses.
Incorrect addition of scrubbing liquid
The wrong addition of scrubbing liquid can substantially reduce scrubber performance. For example, if ammonia is being diminished with sulfuric acid as the neutralizing agent, inlet readings can be lower than outlet readings when pH is not sustained.
Incorrect pump size
The pump’s flow rate and, subsequently, its efficiency suffer when additional items like basket strainers are not considered in the system’s design. In the pump’s design, three factors must be considered. These factors are friction losses across fittings and piping, pressure losses in the nozzles, and pumping height.
Inadequacy of sump fluid replacement
Scrubbers use blow-down or overflow to keep a fresh solution. The scrubber’s speed to keep the fresh solution must be sufficient to sustain the concentration gradient between the gas and liquid stages. If this concentration gradient is inadequate, the system’s efficiency can reduce rapidly and considerably. In some cases, a low gradient results in the removal of the solution’s contaminants. When this case occurs, the tested outlet concentration’s loading is higher than the inlet loading of a specific pollutant. Although the overflow method is more common, if the device uses a blow-down process and this process is inadequate, biological growth, the rate of scaling, and sedimentation will increase. In both methods, constant monitoring of concentration gradient is necessary since evaporation losses may fluctuate radically depending on atmospheric conditions and system size. Thus, the freshwater make-up rate must be ample since the re-circulation piping must discharge at a specific rate to offset evaporation losses.
Incorrect position of the pH probe
The position of the pH probe against the position of the chemical supply injection is a general error of pH control systems (Hankinson, 2018). When the chemical injection pipe is within 12 inches from the position of the pH probe, a proper reading of the pH of the scrubber liquid does not appear since the chemical injection on/off switch and the pH controller shall constantly trail each other.
Insufficient packing depth
A mismatch of shell sizes results in non-uniform liquid distribution. (Yap, 2005). Small scrubber shells must use small packing. However, scrubbers with greater packing depth perform better since more packing surface increases the absorption rate. The additional surface produces more gas-liquid contact.
Nozzle Selection
Nozzles should be selected according to the type of pollutant gas, the chemical formed at the end of the neutralization reaction and the wetting area. The rate of sprayed solvent to pulverize is an important parameter. If the droplets are not pulverized as required, the desired cleaning efficiency cannot be achieved. If the droplet size is lower than the calculated value, sufficient time will not be provided for the solvent to react. This situation causes the system efficiency to decrease.
Packing Material
The packing materials are designed to provide a continuous wet and wide contact area. Packing shapes have a positive effect on mass transfer. At the researches shows that random placement of packing materials is much more effective in mass transfer than regular placement. The geometry of the packing material and the materials made of vary. There are varieties such as ceramic, stainless steel and polypropylene. Plastic packing materials are often preferred because they are both lightweight and resistant to acids and bases. In places where the pollutant gas reacts with the solvent (packing area and packing – nozzle cavity), the packing material selection and height, as well as the height of the nozzle, must be accurately calculated in order for the neutralization to be complete. Insufficient wetting area causes the escaping gas to escape without adequate cleaning.
Temperature
Temperature is an important parameter that must be measured at the scrubber inlet and outlet. Too high inlet temperature causes solvent loss. It also negatively affects the chemical reactions that will occur in the unit. On the other hand low temperatures make the reaction more difficult and cause a efficiency drop.
Written By: Rıza Altunergil, VP Äager GmbH
References
Danzomo, B. A., Salami, M. J. E., Jibrin, S., Khan, M. R., & Nor, I. M. (2012). Performance evaluation of wet scrubber system for industrial air pollution control.
Hankinson, K. (2018). Critical factors affecting wet scrubber performance. Plating Home.
Kastner, J. R., & Das, K. C. (2002). Wet scrubber analysis of volatile organic compound removal in the rendering industry. Journal of the Air & Waste Management Association, 52(4), 459-469.
Kim, H. T., Jung, C. H., Oh, S. N., & Lee, K. W. (2001). Particle removal efficiency of gravitational wet scrubber considering diffusion, interception, and impaction. Environmental engineering science, 18(2), 125-136.
Sreeram, V et al., (2015). Factors that affect the performance characteristics of wet cooling pads for data center applications. 31st Thermal Measurement, Modeling & Management Symposium (SEMI-THERM), pp. 195-202, DOI: 10.1109/SEMI-THERM.2015.7100160.
The United States Environmental Protection Agency. (2020). Monitoring by Control Technique – Wet Scrubber for Particulate Matter.
Yap, L. J. (2005). Evaluation of wet scrubber systems.
21 September 2021