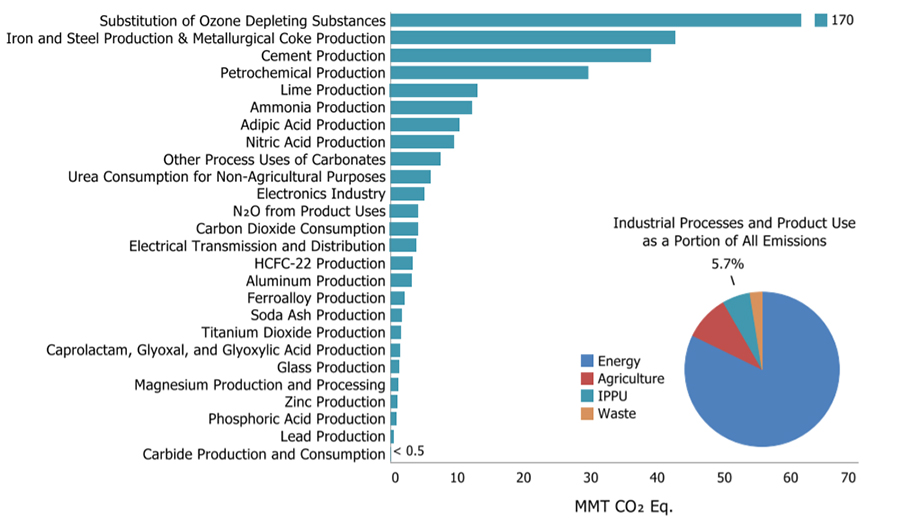
1. Introduction
In parallel with the rapidly increasing world population, unplanned industrialization, nuclear tests, regional wars, the increase in the use of chemicals such as pesticides, artificial fertilizers and detergents etc. used to increase productivity, environmental pollution is also increasing significantly. The issue of environmental pollution, which includes different subheadings, is one of the biggest problems that humanity is struggling with today.
Air pollution, which is also the trigger of global warming, is another issue that needs to be dwelled on seriously. Chemicals such as CO, SOx, NOx, VOC, heavy metals, acid aeroceles released to the nature as a result of the applications of industrial facilities have destroyed 40% of the ozone layer, according to the data of the World Meteorological Organization. Industrial sources of these chemicals that create greenhouse gas effect are presented in Table 1. These pollutants also have many negative effects on human health.
Table 1. Industrial processes and product use greenhouse gas sources
In the light of these data, it has become extremely important for the institutions responsible for environmental pollution to make legal regulations on the environment and to take precautions for the damages caused by industrial facilities. This effort to take precautions has also revealed the need for new equipment of the companies.
Scrubber units, especially known as gas scrubbers, are one of the most efficient systems used to reduce emissions in the form of odor, soot, dust, vapor and aerosol emitted by pollutants to the atmosphere below certain limit values.
2. Working Principle of Scrubber
Gas scrubbers are widely used systems in both industrial and experimental gas cleaning processes due to their high efficiency. It has different configurations in terms of design and operation; It can be used for the removal of gaseous pollutants (H2S, NH3, etc.) as well as the removal of particles that can be contained in the gas.
In a study conducted in 2010; A scrubber has been developed to remove sulfur dioxide from flue gases. The effects of the gas flow rate on the pollutant removal rate in the system were examined.
One of the parameters affecting the removal efficiency in gas scrubbers is the pH value of the solution used as a scrubber liquid. In a study conducted in 2008, it was observed that the removal efficiency increased from 20% to 99% by increasing the pH value of the solution from 7 to 10.
3.Types of Gas Scrubbers
Gas scrubber systems, in terms of different designs; gas phase, liquid phase, gas phase and liquid phase are divided into three. Venturi, plate, orifice gas scrubbers can be given as examples of gas phase ones. Spray and filled scrubbers are classified as liquid phase scrubbers. Cyclonic and dynamic gas scrubbers are in the gas and liquid phase scrubbers group.
3.1. Venturi Gas Scrubbers
The dirty gas enters the system from the junction section and when a narrowing occurs at the throat point, the speed of the dirty gas increases. A turbulent mixing occurs as the dirty gas moves at a higher velocity at the throat point. Gas flow can be approximately 90,000 m3 / h in venturi scrubber systems with a circular neck section. At higher gas flows than this value, it is difficult to maintain a uniform fluid distribution unless baffle plates are used. Venturi scrubbers with a rectangular, long and narrow neck have also been developed for high flow gas flows.
3.2. Plate Scrubbers
Such scrubbers consist of plates placed horizontally in a vertical column. Perforated plates, impact type plates, sleeve type plates and valve plates are common plate types used in this type of scrubber. In perforated plates, the void ratio is approximately 1800-1900 holes / m2. The gas stream breaks up the sprayed liquid, creating droplets of 10-100 μm in diameter.
3.3. Spray Scrubbers
It has a very simple structure in terms of design and its working principle is based on spraying the washing liquid through nozzles into an empty cylindrical column. It exhibits a more favorable situation for the retention of particles of 10-25 μm size. The retention efficiency of gaseous pollutants can be improved by increasing the number of droplets or the liquid-gas ratio, but in this case operating costs may increase.
3.4. Packed Scrubbers
The scrubber consists of a cylindrical column with a feed with inert solid materials (fillings). The liquid from the pure solvent or solution containing the solute is spread over the fillings with the help of a dispersant and wet the surface of the fillings evenly.
Dirty gas enters the diffusion cavity under the fillings and rises up through the fillings. Fillers provide a large area between liquid and gas and a very close contact surface between phases. The dirty gas is absorbed by the liquid entering the tower and the diluted gas is separated from the top.
The gas enters the tower from the bottom, is distributed homogeneously into the filling by means of a distributor (distributor) under the filling, and while moving upwards through the filling, it contacts with the liquid film on the filling surface. The inlet pressure of the gas is higher than the outlet pressure at the top of the tower, and due to this pressure difference, the gas moves upwards. With the nozzle that provides sprinkler distribution at the liquid column inlet, the filling grains are homogeneously distributed on the surface and move downwards with the effect of gravity.
Basic design parameters of structural filled scrubbers can be listed as hydrodynamic flow characteristic, geometry of the filling material, residence time, liquid-gas ratio, pH of the liquid and reactivity. These parameters should be taken into account in the design of scrubbers in order to reduce investment and operating costs.
In order to achieve high efficiency pollutant removal, the following factors should be considered in the design of a scrubber:
- Providing sufficient surface contact area between gas and liquid
- Creating a good liquid gas mixture
- Ensuring sufficient contact time between liquid and gas
- Selection of Light Filler
- Too much surface area of the filling material
- Low solubility of the gas in the liquid phase
- Low amount of liquid retained by the filler
- Chemically inert filler
- Include suitable paths for both streams without pressure drop or excessive fluid retention
Raschig rings are the most used as tower fillers. It consists of cylindrical rings whose height is equal to its diameter, and the thickness of the walls varies depending on the type of material (Stainless steel, polypropylene, ceramic). They are the best tower fill materials in terms of weight per unit volume, free volume, free cross-sectional area and surface per unit volume. Berl saddles are saddle-shaped materials made of porcelain and are filled randomly in the towers. Their superiority over others is that they offer very low frictional resistance against gas flow and have sufficient gas-liquid contact surface. Spiral rings; These rings with a spiral chamber inside are completely similar to Raschig rings, the spiral chamber covers the ring section completely or partially. These rings are always lined up in regular rows and are never filled indiscriminately into the tower.
References
- Intergovernmental Panel on Climate Change (IPCC) Special Report of Global warming of 1.5°C, 12, 16-39, 2018.
- Lim K. S., Lee S. H., Park H.S., Prediction for particle removal efficiency of a reverse jet scrubber, Aerosol Sci. Tech, 2006, 37, 1826-1839.
- Jung S. H., Jeong G. T., Lee G.Y., Cha J.M., Park D. H., Simultaneous removal of SO2, NO and partivulate by pilot scale scrubber system, Korean J. Chem. Eng., 2007, 24(6), 1064-106.
- Joseph G.T., Beachler D.S., Scrubber Systems Operation Review, North Carolina State University, SI-412C,25-63,1998.
- Lee B., Lee C.K., and Lee D.S., Development of an automated diffusion scrubber-conductometry system for measuring atmospheric ammonia, Bull, Korean Chem. Soc., 2011, 32(6), 2039-2044.
- Lehner M., Hoffman K., Geipel W., Hydrodynamic and mass transfer characteristic of a novel grid-structured plastic packing, Heat mass transfer, 2011, 47, 1035-1041.
- Courvert A., Sanchez C., Laplanche A., Renner C., Scrubbing intensification for sulphur and ammonia compounds removal, Chemosphere, 2008, 70, 1510-1517.
- Panza D., Belgiorno V., Hydrogen sulphide removal from landfill gas, Process Saf. Environ. Prog, 2010, 88, 420-424.