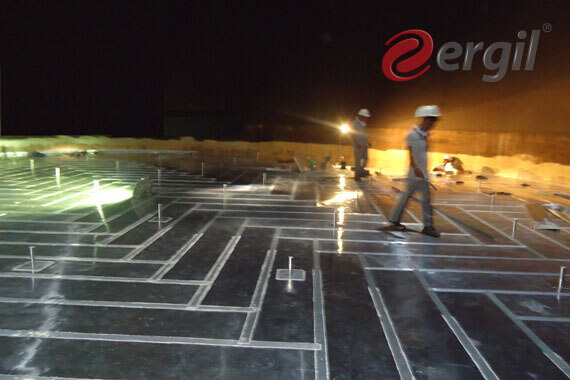
Global warning is happening. According to the World Meteorological Organization every year from 1986 to 2013 has seen annual average global land and ocean surface temperatures above the 1961–1990 average. The evidence is plain. Canada was once covered by the Laurentide ice sheet, but scientists have confirmed that the ice is melting at twice the rate it was 50 years ago, and this is true also of the ice sheets in Antarctica and Greenland. The early arrival of the seasons has visibly occurred within people’s lifetimes, as witnessed through the flowering of plants.
The majority of people and governments attribute global warning to the effects of industrialisation and the discharge of carbon dioxide, methane, ethane and other volatile organic compounds (VOC) into the atmosphere. A minority denies this and believes it is caused by external factors operating on the natural climatic system such as volcanic eruptions, solar activity and velocity variations in the orbit of the Earth around Sun, which have, over tens of thousands of years, led to the heating and cooling of the Earth’s atmosphere.
Let the protagonists debate it. The pragmatists must take action. Global warming is not good for human life, and whatever the reasons, the petroleum industry amongst others has a duty to minimise its effect and slow it down. Also, VOCs are injurious to the health of employees, and most national environmental agencies have regulatory frameworks inflicting heavy financial penalties for breaches of emission discharge licenses.
Since 2005, the Texas Commission on Environmental Quality (TCEQ) has been using infrared (IR) cameras. Rosario Torres, air section manager of the Corpus Christi region says that the cameras make us more efficient. “A site might look perfectly normal to the eye, but then we look at it through the camera, and suddenly we see things that we’ve never been able to see before. It allows us to pinpoint our investigative and enforcement efforts.”
The camera provides real-time images by inverting the physics of fugitive gas leak, making the vapor appear as “black smoke”.
The camera technique used by TCEQ does not quantify the volume of vapour emissions, but provides the Commission with a priority list of tanks to investigate. When installing a new storage tank retrofitting and external or internal floating roof, anticipated emission reductions are usually estimated using API-2517 Evaporating Losses from External Floating Roof Tanks, API-2519 for Internal Floating Roof Tanks or the computer program E&P Tanks.
At the 15th U.S. EPS Annual Emission Inventory Conference held in 2006, a Paper Measuring Fugitive Emissions of Hydrocarbons at Gas Processing Plants presented by Allan Chambers, P.Eng. of the Alberta Research Council Inc., reviewed estimated emissions vs. measured emissions using the DIAL method.
The investigation found that there was a big difference between the calculated volume loss and the actual loss. Fixed roof storage tanks are by far the main source of vapour emissions, however except where product emissions are low, they are no longer being constructed for petroleum products. Existing fixed roof tanks are being modified.
To protect the tank during operating cycles, Äager has developed a full range of spring and weight-loaded pressure-vacuum relief valves (PVRV), flame arresters, gauge hatches, and roof manholes. Replacing the open vents on a fixed roof vertical tank with PVRVs enables the internal tank pressure to remain equal to the external atmospheric pressure. Hassan told Tank Storage Magazine that this alone would cut the loss of product by 30%, and depending on the location of the tanks, the vent can be equipped with a flame arrester or the discharged emissions piped to a vapour collection tank or flared to atmosphere. Both are features that will enhance safety, and improve the profitability of the terminal.
Hassan explained, “Our full contact sandwich or composite IFRs are compliant with API 650. The upper and lower skins are made from aluminium tread plate, and the filling is polyurethane/polyisocyanurate (PU/PIR) foam or aluminium honeycomb composite.
“The PIR material is essentially modified hard PU foam that has improved fire resistance and insulation, properties that satisfy the many International standards, including NFPA 11 Standard for low, medium, and high-expansion foams. Its closed cell structure is unaffected by petroleum products. The panels are dimensionally stable, and have a low thermal conductivity that will help to maintain product temperatures in the tanks.”
As an alternative to the PIR composite filler, Hassan said that the Company also supplies the IFRs with an aluminium honeycomb structure, which exceeds 1000 pockets per square metre, it has acquired a structural strength that is greater than API 650 (H4.2.1.4) requirements. He said, “It is really a question of customer preference, as both function in the same way. The aluminium sandwich honeycomb structure is stronger and will not bend. It will provide a longer life; but for that, one pays around three times the price of the PIR sandwich panel.
“The annular space between tank shells is sealed by a primary seal and secondary wiper seal that effectively close the gaps, reducing VOC emissions and losses of the stored product.
It is generally accepted within the industry that floating roofs are the most cost-effective way to reduce vapour emissions, providing that the products being stored have a vapour pressure less than 34.5 kPa. Floating roofs are not recommended if the vapour pressure is greater than 76.6 kPa, as at that pressure the product is subject to vapour losses due to flashing.
Installing a disc the diameter of a storage tank in a closed vessel begins to look a lot easier than it first appeared. “Floating roofs are simple to install,” said Aydin Dogan, senior installer based at Äager’s factory in Mersin, Turkey. “Every IFR is designed to match the specific tank it is to fit, such as any incline, and the pitch of the cone. They are manufactured in small pieces that will fit through a 20 or 24-inch storage tank manhole cover, and are assembled in the tank. It’s very much like a jigsaw puzzle, with all the pieces clearly marked. There isn’t any need for special tools or cutting equipment.
“As the manufacturing and the installation of the IFR is fairly quick, the tank need not be out of service for very long,” he concluded. The IFR includes adjustable roof support legs that are set to low-level for product discharge or at a suitable platform height for tank cleaning operations.
The Company also manufacturers the traditional pontoon type IFR, which consists of a series of capped hollow tubular pontoons connected to a grid of beams and top-sheet of aluminium tread plate. The design permits a vapour space between the floats and the underside of the plate. It remains a popular design; but is beginning to lose favour due to its higher cost, and the benefits offered by the full contact IFRs.
“Global warming is going to create the need for changes in the storage industries,” enthused Hassan. “Long periods of high ambient temperatures, increased rainfall and wind speeds all affect vapour leakage rates. As an industry we are going to have to look at the design of seals and wiper blades, and we have a few ideas in those areas that are currently being investigated. External surface finishes and insulation are also areas open for re-evaluation. As an engineer, the next 10 years at Äager are going to be a challenging and interesting time.”
(Tank Storage Mafazine, July / August edition)